Magnetic strength & depth of magnetic field are heavily linked to the physical size of a magnet. Indeed, the bigger the magnet, the greater the magnetic field. Oversizing a magnet for a magnetic separation application to increase the likelihood of extracting contaminants or to increase the service life of the magnet or to just be ‘on the safe side’ may in fact do more harm than good.
So why is installing an oversized magnetic separator a bad business decision?
There are two main reasons why having an oversized magnetic separator is a poor decision.
1. Cost
- Magnetic strength & depth of magnetic field are heavily linked to the physical size of a magnet. Indeed, the bigger the magnet, the greater the magnetic field. Oversizing a magnet for a magnetic separation application to increase the likelihood of extracting contaminants or to increase the service life of the magnet or to just be ‘on the safe side’ may in fact do more harm than good.
- Industrial Magnetic Separators are not only large, they are also very heavy and therefore attract significant shipping/transport, infrastructure & installation costs. Bigger the magnet, the more they cost to transport, suspend & install.
- Electromagnets (the preferred magnet for troughed belt applications) require power for operation, and their power consumption and subsequent ‘running costs’ are proportional to the size of the electromagnet. The bigger the magnet, the more they cost to run.
2. Performance
- There is no performance advantage from intentionally selecting an oversized magnetic separator. A correctly sized magnet will reach to the bottom of the burden pile to extract contaminants. An oversized magnet will also reach to the bottom of the burden pile to extract contaminants. There is zero return on the extra investment in selecting an oversized magnet.
- An oversized magnet will not only reach the bottom of the burden pile, it will also reach well beyond that. This “extra reach”, can actually result in greatly reduced magnet performance and practically deliver the same performance as an undersized magnet.
Magnetic Separator Oversizing – The Common Causes
1. Flawed Measurement When Specifying A New Application
The most common cause of a magnetic separator to be oversized for a new application is either poor/guessed measurements or intentionally overstated measurements at the time of scoping to allow for unforeseen or worse case scenarios, or for increased comfort regarding expected separator performance. While the measurements regarding conveyor belt width, troughing angle etc are sometimes well known, others such as burden depth and lump size often are not as well known and there may be a temptation to overestimate these figures just to be sure. Overstating burden depth & lump size is almost certain to result in an oversized & higher cost magnet being specified for the application.
2. Flawed Installation When Redeploying A Magnetic Separator
Magnets are relatively uncomplicated devices that, on face value, can be easily redeployed as & when required. While it is definitely true that magnetic separators can be easily redeployed to an alternative location or even alternative application, appropriate scoping of the new location/application is often overlooked. Unless the magnetic separator is being redeployed to an identical conveyor, running the identical burden depth & identical lump size, then there is a likelihood that the magnet will not be installed to meet the application requirements.
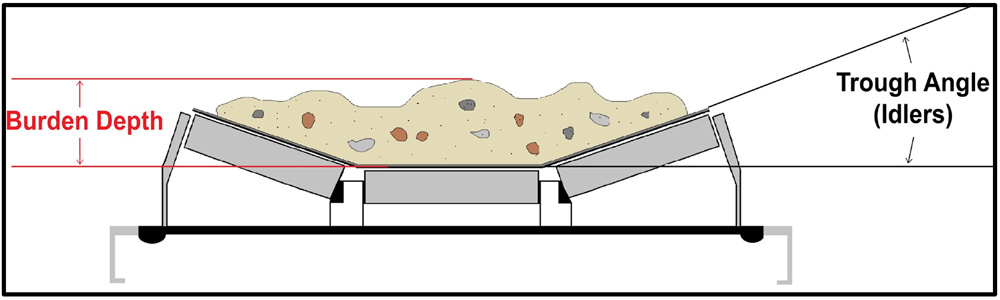
What are the practical impacts of having an oversized magnetic separator?
The single largest issue with having an oversized magnetic separator is that large magnets generate a magnetic field that is deeper than the conveyor frame. Over a period of time, the section of the conveyor frame directly under the magnet becomes magnetised from the continued exposure to a high strength magnetic field.
1. Loss of Magnetic Separator Performance
Having a magnetised conveyor frame results in a section of the frame behaving as a magnet that emits its own magnetic field. This newly created magnetic field is generated from underneath the burden pile, whereas the magnetic field from the magnetic separator is generated from above the burden pile. The two magnetic fields oppose each other as one magnetic field attempts to pull contaminants upwards, away from the belt, while the other newly created magnetic field attempts to pull contaminants downwards, towards the belt. The overall effect is that contaminants do not get removed from the belt, which may result in significant issues like stoppages & equipment damage further upstream.
2. Increased Maintenance Costs
The section of the conveyor frame that has become magnetised will attract anything with metallic content to its surface. Unless removed, those items then also become magnetised. As objects continue to ‘cling’ to the conveyor frame they eventually begin to cause increased wear on the belt & other equipment.
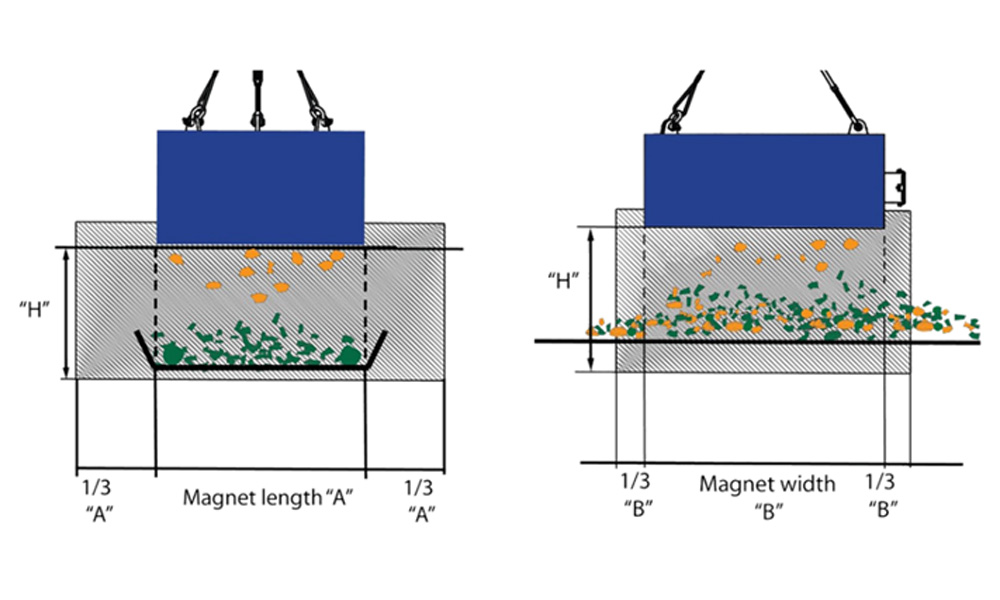
Above: Illustration of the areas defined as the “Magnetic Zone” (shown as the shaded area). Any metallic items including conveyor frames/stringers, pulleys, etc located within this zone will become magnetised over time.
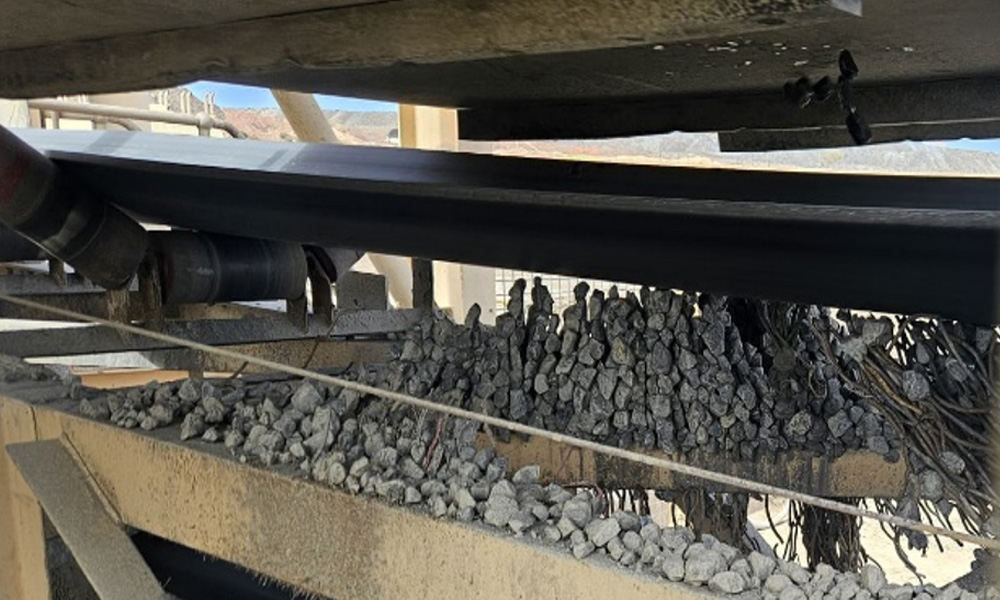
Above: Classic signs that the magnet is oversized for the application & the surrounding environment has now become magnetised.
What can I do to ensure my magnetic separator is the correct size for the task?
1. Measure Correctly
Avoid the temptation to approximate or overestimate key specification details like belt width, trough angle, conveyor speed, burden depth, or lump size. The accuracy of these measurements is completely relative to the suitability of the magnet.
2. Expert Supply & Installation
While magnets look simple enough to install and operate, the consequences of getting it wrong can lead to underperformance and wasted investment. Magnets need to be installed correctly and according to the manufacturers precise requirements to ensure maximum possible performance without causing any detrimental effects such as magnetisation of the conveyor frame.
3. Expert Advice & Testing for Magnetic Separator Relocations
Magnetic Separator redeployments are more successful if they are first ‘scoped’ for the redeployment rather than just moved to a new location. Before redeploying a magnetic separator, you should seek the input of trained professionals that can assist with scoping the solution and suspension configuration to suit the application. Prior to redeployment, magnets should be tested for magnetic strength by suitability trained and skilled personnel to establish the equipment operating parameters & performance.
Accurate Industries has partnered with DINGS magnetic group from the USA. DINGS has over 120 years of experience in the manufacture of the highest quality industrial magnetic separators. Accurate Industries staff have the skills, experience & test equipment to assist with your Magnetic Separator scoping, supply, installation or servicing needs. We would be more than happy to help, so please get in touch.