It is often true that Belt Weighers are serviced, checked and calibrated more frequently than traditional scales like weighbridges/truck scales, platform/floor scales or hopper/silo scales. In some circumstances, Belt Weighers are serviced, checked and calibrated two, three or even four times as often as other scale types.
For example, a large high traffic weighbridge for oversized vehicles at a mine site or quarry would likely have the following periodic service schedule.
- 1 x 12 Monthly calibration with certified masses
- 1 x 6 Monthly performance check with a known mass
- 2 x 6 Monthly routine service on all wearing parts
In contrast, a high capacity, high throughput belt weigher at a mine site or quarry would likely have the following periodic service schedule.
- 4 x 3 Monthly calibration with built in masses
- 3 x 3 Monthly routine service on all wearing parts
- 1 x 12 Monthly routine service & idler alignment
- 1 x 12-24 Monthly replacement of all weigh zone rollers
So why does a belt weigher need so much attention? If considering a belt weigher versus a common scale like a weighbridge, it really comes down to two key factors: the type of Application (STATIC or DYNAMIC) & the type of Mechanical Installation (ISOLATED or ATTACHED).
What type of application is a Belt Weigher anyway? Static or dynamic?
There are many, many different types of scales used in domestic, commercial and industrial applications every day throughout the world and despite many stark differences, they all mostly fall into one of two categories: STATIC or DYNAMIC. The differentiating factor between a scale falling into either static or dynamic category actually has very little to do with the scale electronics or mechanics but is more attributed to how the product being weighed is presented to the scale.
So, in simple terms…
Scales that are used in STATIC applications start with an empty scale, have the product to be weighed applied to the scale, the product comes to rest (i.e. stationary…not moving….STATIC), a weight measurement is captured, the product is removed from the scale leaving it empty.
Scales that are used in DYNAMIC applications start with an empty scale, have the product to be measured applied to the scale in a continuous manner, the products never come to rest while a weight measurement is being captured (i.e. not stationary…..always moving….DYNAMIC), the product is eventually removed from the scale leaving it empty.
Scales like weighbridges, hopper scales and floor scales are all STATIC scales, and a Belt Weigher is clearly a DYNAMIC scale. Most scales in use in industry today are STATIC type scales and are used for a broad range of typical applications like weighing trucks or pallets, whereas DYNAMIC scales are generally used for specific purposes like high speed and/or high throughput weighing where there is simply no time or practical ability to stop a process to capture weight information.
ISOLATED, ATTACHED or IT’S COMPLICATED….
The second key factor relates to whether the measurement mechanism (the bit that has the product being measured on it) is ISOLATED or ATTACHED to the surrounding environment. Almost all scales have a weighing mechanism that is ISOLATED from the surrounding physical environment. This area is sometimes referred to as the “Live Zone, the Scale Bed, Live Platform, Weigh Zone or the Weigh Platform” of the scale, and a key principle of accurate weigh measurement for almost all scales, is that the weigh platform be free standing and clear of any objects resting on or touching the weigh platform. Traditional STATIC scales are all ISOLATED, however Belt Weighers are both DYNAMIC & ATTACHED.
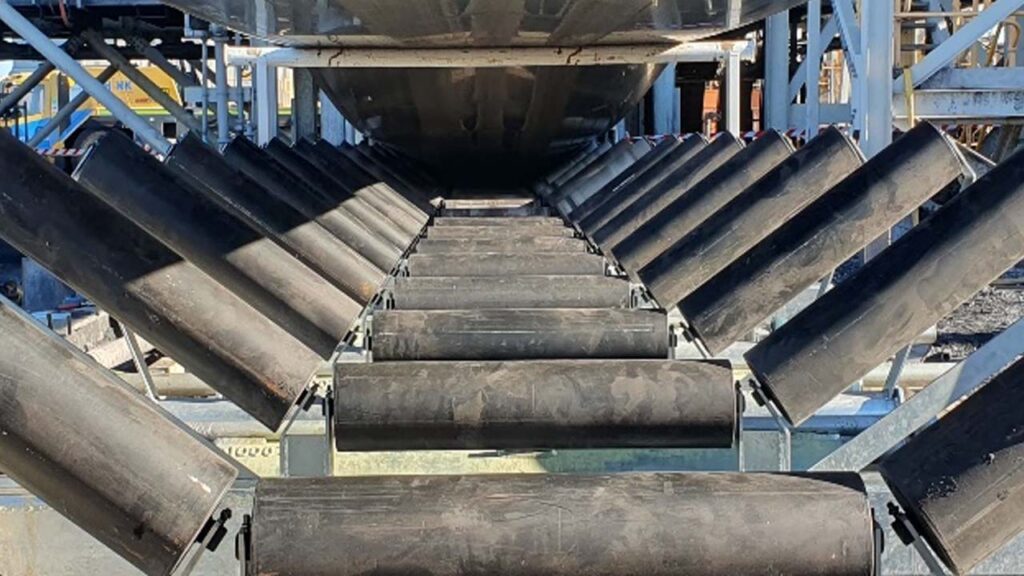
The service and maintenance implications of being dynamic and attached
Belt Weighers are physically connected to their surrounding environment, and specialist equipment, care and maintenance is required to ensure that these types of scales can operate properly – Belt Weighers are no ordinary scales.
Most modern Belt Weigher designs incorporate a ‘floating deck’ design to give the weigher the best chance of capturing accurate weights. This design helps to reduce some of the influencing effects from the immediate environment (like vibration). The idlers and rollers that sit on top of the weigh frame are constantly influenced by the conveyor belt – there is no isolation – worse still, the connection between the weigh frame rollers and the underside of the conveyor belt is not firm and fixed, but inconsistent and subject to belt tension. This also means that the conveyor belt itself actually becomes part of the live scale and therefore needs to be included when performing routine service and calibrations. This is also true for the idler frames and rollers that lead in and lead out of the weigher frame. Even though the lead in and lead out areas do not contain any weight sensors, the entire area (Weigh Zone) needs to be considered as if it were a scale and serviced and adjusted accordingly.
Belt weighers are equipped with sophisticated integrators/controllers that operate advanced algorithms to compensate for inertia, angle of incline and a host of other factors. However, even the most forgiving integrator with the best features will still require the physical environment surrounding the belt weigher to always be in ‘Weigh Quality’ condition during operation.
Key takeaways
- If you are not having your belt weigher checked, serviced and aligned regularly, you are likely to be exposed to an increased likelihood of false rates and tonnages.
- Beware of ‘perfect’ test results from service providers. Critical elements such as belt tension variation, roller wear or build up, belt wear/inconsistencies, belt speed fluctuations, conveyor frame rigidity and other items can not only affect weighing performance, but they are also constantly changing. There is almost zero chance of a belt weigher having identical performance characteristics after 3 months of heavy usage with typical wear and tear, there are simply too many external influences.